Maintaining Canada’s network of over of public roads from coast to coast is a continual process.
Not only do Canadian roads experience a wide range of climatic conditions that are damaging over time, but North American vehicles are getting larger and heavier, further accelerating deterioration.
According to the (EPA), the average 2020 model-year vehicle weighs almost 30 per cent more than in 1981. Today, electric vehicles can weigh another 30 per cent more than their ICE equivalent.
Traditional road repairs and replacement take time and can impede traffic flows for days and weeks. The work itself results in truckloads of waste materials being hauled away to suitable storage sites. New inbound replacement road materials must be trucked in. Added together, this creates high overall levels of GHG emissions.
(RSR) based in Ajax, Ont., says it has the solution to both the lengthy resurfacing disruptions and the waste and carbons linked to road repair. It’s called Hot-In-Place Recycling (HIR).
Frank Crupi, vice-president of R&D with RSR, told the Daily Commercial News his company has designed and engineered equipment that repairs road surfaces quickly, recycles 100 per cent of the in-place road materials, and creates new road surfaces proven to last 20 years or more. It achieves this with 70 per cent less GHG emissions and at costs far less than traditional methods.
“Asphalt is made of sandstone and a petroleum product called liquid asphalt cement,” Crupi said.
“What happens to asphalt over time is that it loses its light end oils. They turn into fumes and dissipate out of the asphalt cement component. The asphalt goes brittle, which is why it cracks and starts to get potholes. What we do is we put those light end oils back in the asphalt cement. And this can be done over and over and over again. That’s called sustainability.”
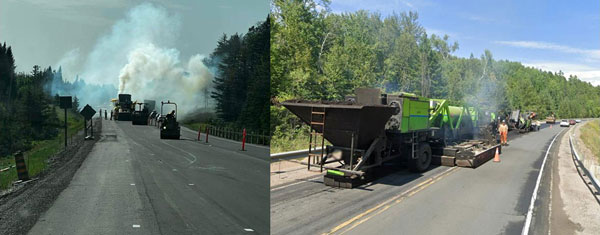
Crupi and his co-founding brother have spent a lifetime in the paving business, he explained, and have been perfecting their recycling road repair process since 1994. Over that time, he said they have completed 18 million square metres of HIR roadwork.
“It’s based on rejuvenation,” Crupi said. “It’s based on bringing something back to life.”
RSR’s “HIR train” utilizes up to 50 millimetres of the worn, aged asphalt surface of a road to produce a new finished wearing surface that is “monolithically bonded.” Instead of tons of old material being trucked away, nothing is removed as waste and no new non-renewable materials are introduced.
Rather than the milling, mining and repaving that can sometimes take weeks, the new HIR-finished road is ready for driving soon after the new surface is laid.
“Hot In-Place Recycling is one multi-function step,” the RSR website says.
All road surface removal, reprocessing and repaving functions are accomplished simultaneously. The process eliminates cold milling and tack coating and does not allow a tack surface to be exposed to traffic.
It produces no Reclaimed Asphalt Pavement waste and minimizes traffic congestion.
On top of all the recycling and reduced disruption considerations, RSR says its HIR process can save governments a great deal of money. Up to 30 per cent more kilometres of road can be resurfaced for the same conventional road resurfacing budget.
Maintaining Canada’s roads is becoming an area of increased importance. Poor roads are costly. The Canadian Automobile Association “poor roads cost the nation’s drivers a total of $3 billion per year in higher operating costs.”
For governments at all levels, the cost to replace those portions of Canada’s road transportation infrastructure rated as being in poor or very poor condition was by Statistics Canada to be $250.2 billion.
At the same time, repair processes need to consider their environment impact.
John Bleasby is a freelance writer. Send comments and Inside Innovation column ideas to editor@dailycommercialnews.com.
Recent Comments
comments for this post are closed